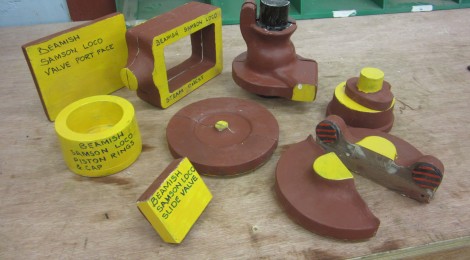
Introducing ‘Samson’ – a new project for the New Year…
Having dropped numerous hints over a number of previous blog postings, I can now confirm that our ‘new build’ steam locomotive project is the Stephen Lewin 0-4-0WTG ‘Samson’, the original originating from 1874 and scrapped, it is thought, some time around 1904.
A brief reminder of Samson’s history might be useful. Samson was supplied, new, to the London Lead Company for use on the one mile tramway to Cornish Hush mine. The line itself has been featured on this blog and can be found by searching ‘Samson’ in the search box that appears at the top right of this page. The locomotive’s effectiveness is not known, but it lasted for a quarter of a century so must have been successful in some way! It almost certainly replaced horse traction and the one known photograph of the engine suggests something of a fuss was made over it when new!
Samson is an interesting railway locomotive, having much in common with a traction engine or steam portable engine. Being single speed it must have been slow, prone to difficulty starting (being single cylindered) and perhaps a little rear end heavy when pulling a train. However, for the work asked of it the simplicity of design would have been an advantage.
I am preparing a lengthy report that will be available via the downloads section later in the year, but in the meantime I will introduce the project itself. Dave Young and I have been talking about this project for some time, and the feasibility of it. Ken Swan, well known model engineer, had also given Samson much thought in the past, with view to making a 7 1/4 inch gauge model of the locomotive.
Dave and I looked at the potential of the project as something ideal for our new Regional Heritage Engineering Centre to build – a great way to put the facility on the map and also a project on which apprentices, staff and volunteers could learn, train and hone skills on. Being a small engine, space would not be too much of an issue, nor handling of even the more substantial components. However, it does require a professional approach as well and so the management will be per our Safety Management System for such work and some specialist services will be needed, such as finalising the boiler design etc.
One thing needed, with any new-build announcement, is credibility. Therefore, to prove the project was feasible, David prepared the drawings for the project and then made the most complicated patterns, for the cylinder block. This gave us confidence and so he continued to produce detail drawings as well as patterns at a furious rate. Meanwhile, I arranged to have the frames, crankshaft and several other components profile cut at no cost to the Museum in order that when we went public (i.e. this post!) we could show we had a feasible project, patterns to hand and a set of frames upon which to build as well as the workshops in which to do it. Happy that this stage has been demonstrated, the project is thus announced and tangible progress can already be demonstrated.
One question the reader is bound to have is ‘how long will this take and what will it cost?’. Timescales are always tricky but Dave and I would like to think we could have something resembling Samson and working, under steam, within three years, maybe sooner. Of course, this depends on finance and I am conscious that in these straightened times, and with a major capital programme looming for Beamish, the Samson project must be carried out as expeditiously as possible – it must be cheap but not create a cheap result! Dave’s considerable input, the use of our own workshop facilities, my own time as project manager and the soliciting of free work and materials all thus contribute to this to the point that I think at this stage we are able to start and over the next 18 months I will look for further support for the project in order to assist in bringing it to fruition.
I hope this provides a useful and interesting summary of this project, as mentioned above a feasibility report will appear online in due course, meanwhile preparation work is ongoing and I would hope that there is something tangible to display in April when we hope to run some limited number tours of the RHEC during the Great North Steam Fair event… As ever, watch this space!
Below: These are the patterns for the motion bracket/slidebar support (left), slidebars (bottom left) and crankshaft brackets (x2 – the pattern has removable components to suit the variations on brackets each side of the boiler). These are complex patterns with numerous challenges and the need for cores and some clever moulding techniques. The reverser stand will be similarly complex, as it includes the pump body for the crankshaft driven water feed pump.
Below: No mistaking the flywheel pattern! Calculations have been done to show that a casting, once machined, is suitable for this purpose (the alternative being a turned solid blank) – there being no flywheel brake to cause heating of the rim and the engine is relatively low speed (and single speed).
Below: The cylinder block (core not shown) – a complicated casting requiring multiple cores. Following our experience with No.18 and the difficulty of accessing the port faces to machine them, Samson will have its valve chest formed from a number of components, which can be dismantled to allow access by machine tools not just for the manufacture of it, but also ongoing maintenance.
Below: A further collection of patterns showing the valve chest assembly, safety valve shroud, cylinder ends, piston and slide valve. There are numerous other patterns also in store ready for use in this project, the overall total representing a considerable number of hours in the making (and, of course, the drawings) and a colossal financial saving for this project. Add to this the use of Dave’s volunteer labour plus the staff hours (who will be learning new skills through their involvement in the project) and it can be seen that many of the usual costs of such a project are absorbed or reduced right from the start – this being a key factor in the decision to even attempt this new-build.
Fantastic – joking aside regarding the Atlantic Z1, my money was on it being a narrow gauge locomotive. Great project
[…] they have up their sleeves this time? I think you'll find the answer here (their next blog post): Introducing ‘Samson’ – a new project for the New Year… Richard Reply With […]
I look forward to following progress on the blog :o)
Who did the casting? Ferrous foundries are few and faw between these days and I am sure that other model engineers would like to know.